Focusing on Process Improvement: A Quick Look
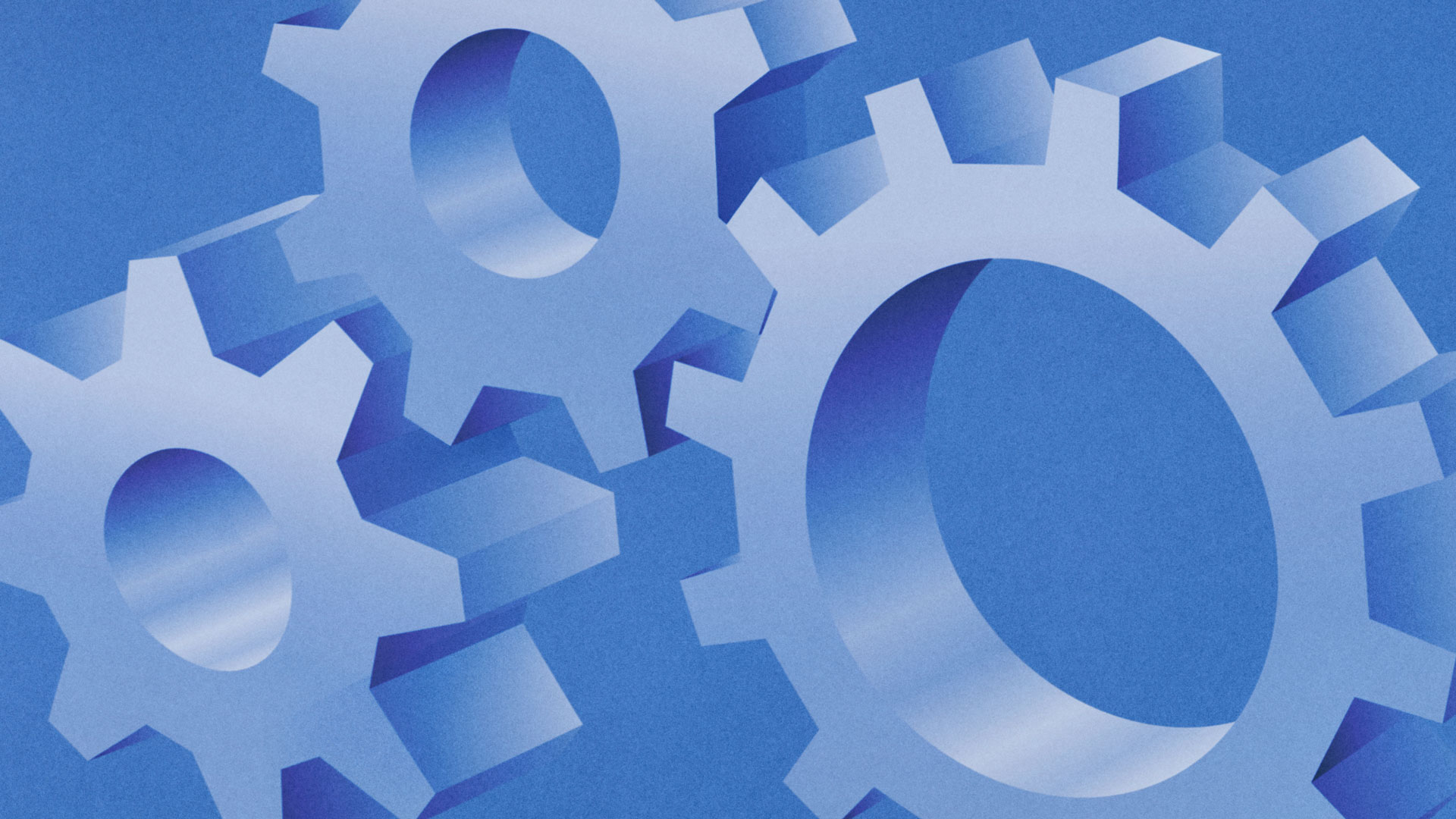
Managers and work team leaders are increasingly looking for ways to improve the efficiency and effectiveness of key work processes, whether they are in manufacturing, service, education, healthcare or government organizations. Thoughtful leaders want to reduce costs and simultaneously increase quality and productivity, whatever the purpose of the organization.
Much of the current process improvement activity is based on learning and doing that comes out the quality revolution of the last 40 years. One of the major understandings that guide effective quality management is the principle of continuous improvement.
Successful leaders know that perfection is impossible yet the effort to improve is a constant in successful organizations. This is based on the reality that there is no steady state in life, either things atrophy and die or they are purposely focused on ways that improve what is done. Leaders that understand this reality commit to following: organizational design principles that are focused on quality and continuous improvement. They avoid critical wastes that cause process failures, wastes or errors, and they use simple but powerful process mapping techniques.
Organizational Design Principles for Quality and Continuous Improvement
1. The Customer Pulls the Process
2. Commit to a Quality First Policy
3. Do only those things that Add Value for the Customer
4. Never Pass on a Problem or Error to the Next Person or Step in the Process
5. Consciously and Constantly Correct, Control or Improve the Method, the Process or the System
6. Develop and Use Reliable Methods to Ensure Process Control
7. Manage by Facts and Data Not Emotion
8. Create a Psychologically and Physically Safe Environment
9. Involve Everyone's Head and Heart
10. Continuously Improve the Method, the Process, the System and the Organization!
Critical Wastes Causing Process Failure Points and Errors
1. Waste of Time - Time out of control
2. Waste of Errors - Doing something 2 or 3 times to get it right
3. Waste of Materials - Using more materials than needed
4. Waste of Idle Inventory - Just In Case Inventory
5. Waste of Transportation - Unnecessary moves or distances
6. Waste of Energy - Using more power than needed
7. Waste of Space - Inappropriate use of space
8. Waste of Overproduction - Producing more than needed
9. Waste of Labor - Too many people doing the job
10. Waste of Complexity - Unnecessary steps or check points
Process Mapping forImprovement
Keeping in mind the design principles and critical wastes noted previously, managers and team leaders that are focused on establishing sound work processes or improving key processes can utilize traditional process mapping techniques listed here.
1. DESCRIBE the process - Note the START and END points first, then list all the current steps in order
2. ANALYZE the process
3. Identify FAILPOINTS, weaknesses, non-value added steps
4. Prioritize HIGH IMPACT FAILPOINTS
5. Identify ROOT CAUSES of high impact failpoints, using a Cause & Effect Diagram
6. Generate IMPROVEMENTS to the process
7. REDESIGN the process
8. Establish an IMPLEMENTATION PLAN
Understanding and utilizing these process mapping steps, along with knowing quality and continuous improvement design principles and being guided by critical wastes causing failure points are the three primary ways to attack work process issues. This article does not imply that successful process improvement can be achieved without understanding, as well as, the use of additional tools and insights.
Measurement Tools
· The difference between End-Result Objectives and In-Process Indicators
· Control & Other Statistical Charts
· Perato Diagrams
· Check Lists
· Cause & Effect Diagrams
This "focused" presentation is intended to serve as a foundation for understanding and doing successful process improvement in any work process in any organization. Paradigm Associates has facilitated "value-added" improvements in universities,hospitals, social services, government agencies and manufacturing organizations.
Continue Reading Additional Articles
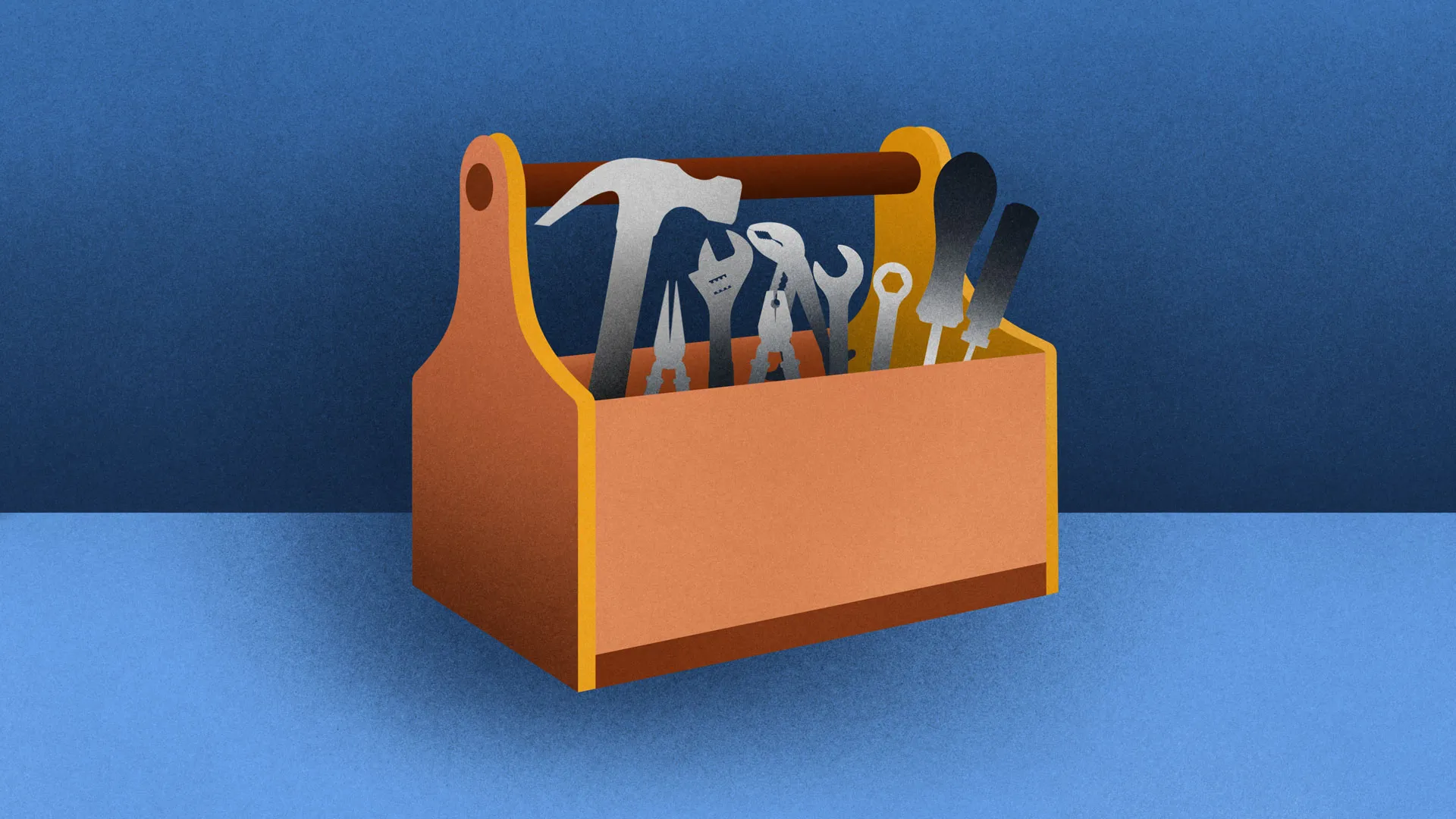
Architecting Success: Strategic Insights for Selecting Your Organization's Ideal Structure
What Makes for Long-lasting Teams?
Improving Employee Performance
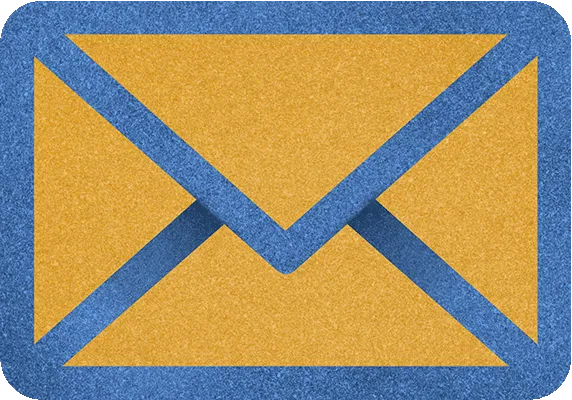
Ready to drive results with tailored strategies? Book a strategic consultation to explore how our insights can elevate your organization.
We’re dedicated to helping you achieve your goals. If you have any questions or feedback, contact us directly by phone or email. Your insights are invaluable in refining the solutions we provide and delivering the results you expect.