Wait! Don't Mess Up Our Process.
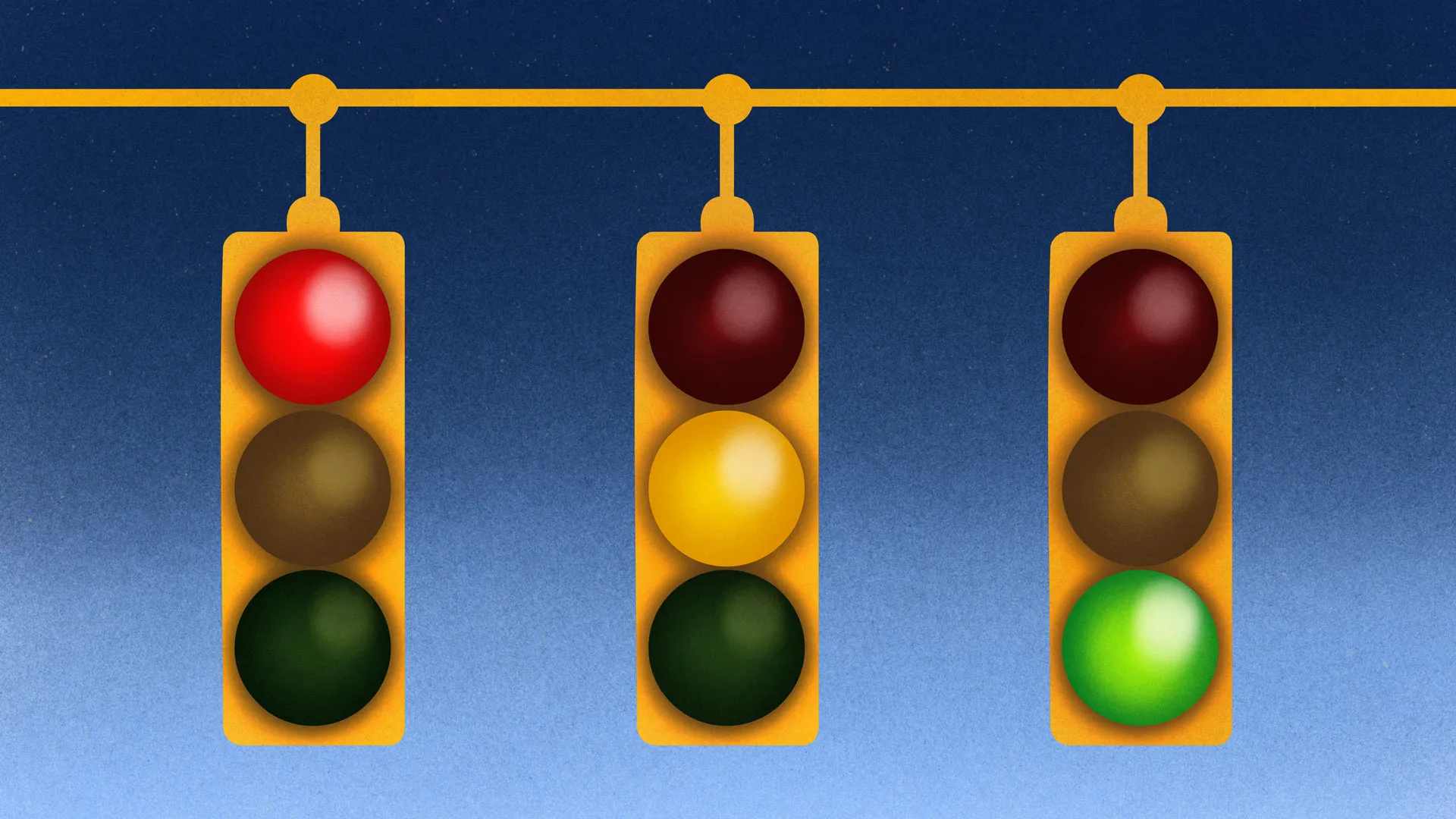
Our crack failure analysis team in Quality Engineering received the first call when a hi-tech manufacturing process started turning out defective products. They rapidly went to work, examining process data, taking measurements, assessing raw materials, asking questions about operators’ training levels, and calming down panicking manufacturing managers. Most often, the team defined the problem and corrected it within an hour or so. The team asked, “What changed?”
However, some of the most frustrating problems to identify and correct fell under the category of innovation. Yes…innovation—when operators responsible for an important step in the process thought they would take the initiative to change the process without asking for permission or telling anyone. Someone had an idea but did not test it or implement it in a controlled way.
We want our employees to be creative and look for improvements, but innovation is a process in and of itself. How do we encourage new ideas? How do we identify the best? How do we test them? How do we implement the best in a systematic, controlled way?
In crucial manufacturing or business processes, innovations should be tested outside the ongoing process. This makes sure the change to a particular step in the process produces the required result in quality and efficiency. After passing that analysis, the step can then be introduced to the ongoing process in a closely observed experiment where all affected participants are aware of the change and on board with it.
Innovation itself is a process. Innovative organizations encourage good ideas and let all employees know how ideas will be collected, evaluated, and put into practice. Recognition and rewards can make this process work in all segments of the organization. Those creative rogues can be exceptional contributors if they have a well-recognized innovation process where their ideas bear fruit.
Continue Reading Additional Articles
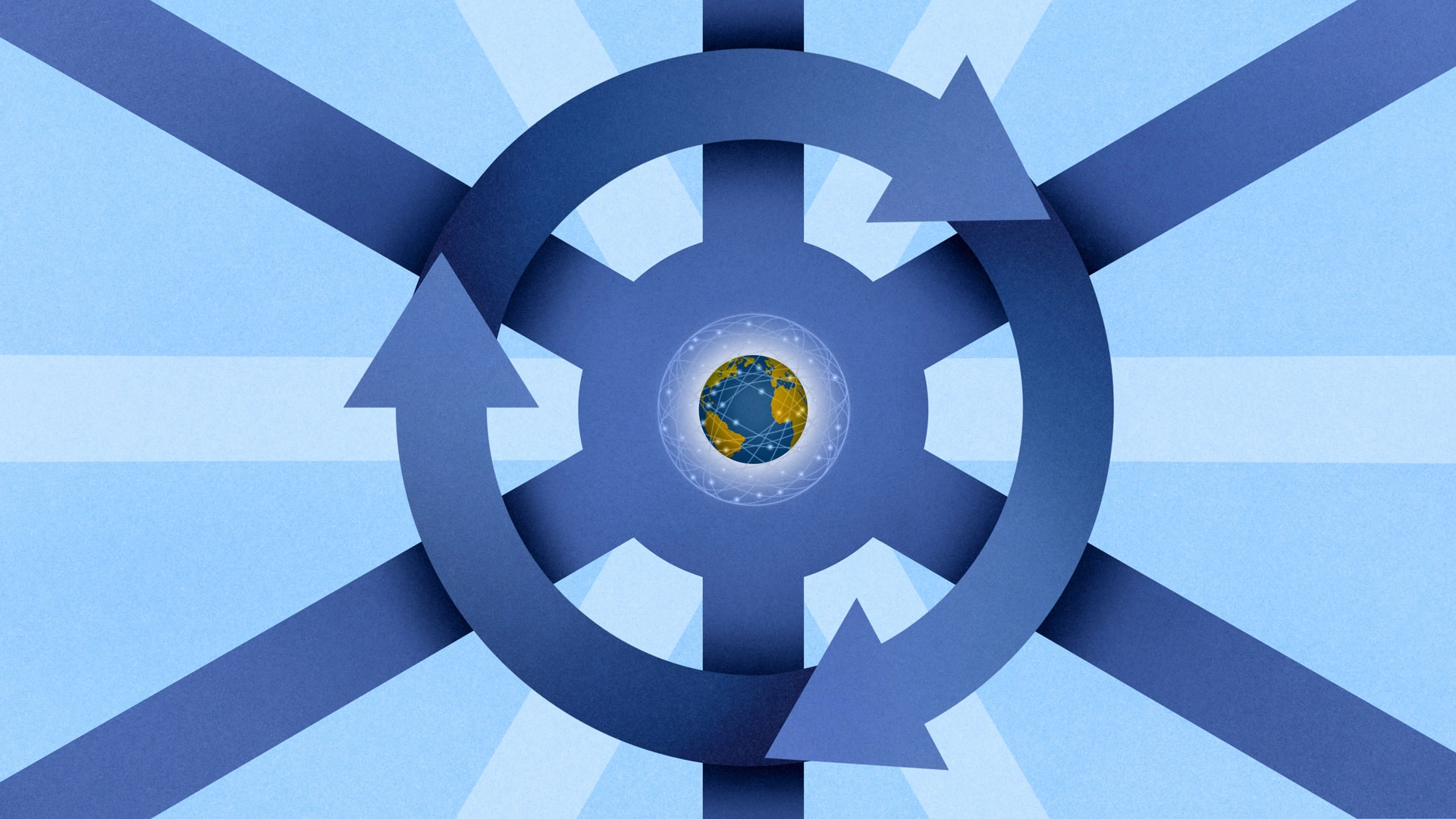
Using Technology to Improve Processes Across the Business
What Makes for Long-lasting Teams?
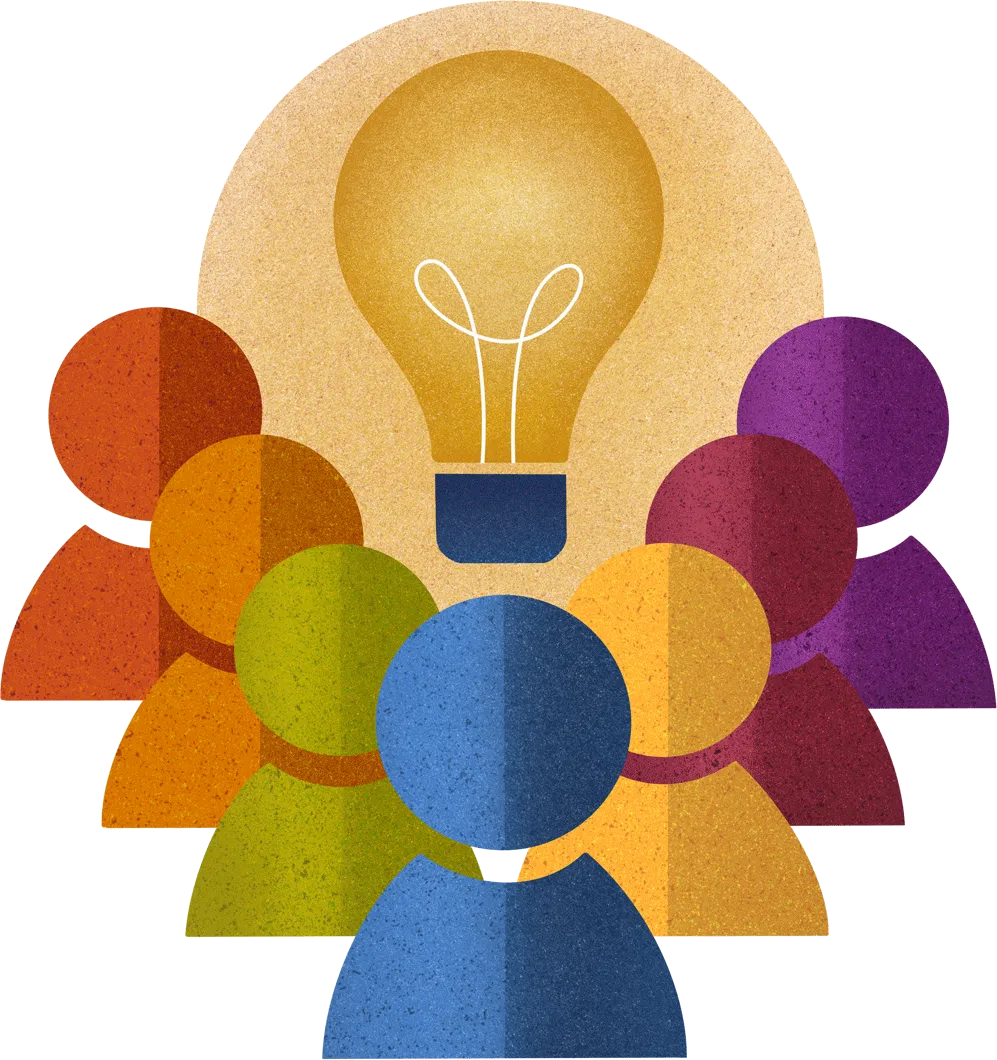
Looking Beyond the Obvious - Construction Partnering Facilitation
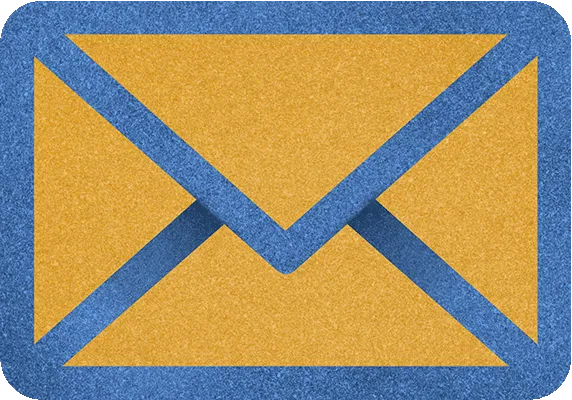
Ready to drive results with tailored strategies? Book a strategic consultation to explore how our insights can elevate your organization.
We’re dedicated to helping you achieve your goals. If you have any questions or feedback, contact us directly by phone or email. Your insights are invaluable in refining the solutions we provide and delivering the results you expect.